Latest articles:
– Hydrogen for energy transition →
– Can hydrogen and the latest burners reduce carbon emissions? →
– Oxy-fuel combustion for decarbonization →
– Decarbonisation of secondary aluminium melting →
Applying Industry 4.0 to non-ferrous
Air Products has been delivering combustion equipment, technology solutions and atmosphere control systems to the non-ferrous industry for over 50 years. We supply to hundreds of customers across the world who produce everything from aluminium and copper, to zinc, lead and precious metals — whatever the product, we're always looking for new ways to help.
We have developed a range or oxy-fuel burners and technologies specifically for rotary and reverb furnaces.
As Industry 4.0 is beginning to shape the way foundries are designed and operated, at Air Products we have created Air Products Smart Technology, a platform that can provide insight into process optimisation by taking advantage of Smart Systems, and incorporating wireless sensors and cloud technology to track key process parameters.
Select your type of furnace to find out the right solution for you:
History
Air Products and the non-ferrous industry
Technology, development and innovation are central to Air Products. Our history and culture is shaped around developing long-lasting relationships with our customers based on an understanding of their needs, integrity in the way we do business, and a passion for exceeding expectations. These close working relationships have helped to shape the way we work today and how we will continue in the future.
Our story dates right back to the 1970's when we launched the first of many innovative solutions for the non-ferrous industry:1970's | 1980's | 1990's | 2000's | 2010's | 2020's | Future . . .
1970's
Multi-flame burners
Air Products developed its first range of water-cooled, multi-flame burners for use with natural gas or oil.
Industry fact
1972 - Aluminium recycling began - Since 1972, an estimated 660+ billion beverage cans have been recycled—placed end-to-end they could stretch to the moon nearly 300 times!
1980's
K-Tech
Our two medium momentum flame K-Tech burners are launched - one non-water cooled version, and one supersonic water-cooled.
Air Products' EZ-Fire was launched. EZ-ily retrofitted to existing air-fuel burners, this non-water cooled burner had a high momentum flame for natural gas.
Industry fact
1981 - Formation of the European Aluminium Association (EAA).
1990's
M64
Air Products' M64 (GKM) Burner is launched. This revolutionary burner technology featured a low momentum luminous flame and tube-in-tube configuration.
EZ-Fire LN
Our first low NOx burner, the EZ Fire LN launched. A non water-cooled, air-oxy fuel burner uniquely featuring a high momentum flame (in air-fuel mode) and a low momentum flame (in oxy-fuel mode).
RILEE® introduced
We introduced our state of the art RILEE® combustion system for direct fired reverb furnaces. The technology featured a hot-gas re-circulation fan for optimal organic matter burn-out.
LEAM™ launched
Air Products' LEAM combustion system launched. An environmentally friendly solution for melting contaminated aluminium scrap in a rotary furnace with the additional benefit of reducing fuel consumption.
2000's
During the 2000's Air Products concentrated it's efforts on design and development of it's next generation melting technology, launched in early 2010's
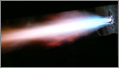
We began the development of our Uniform Heating Burner for reverb/reheating furnaces. A proprietary flameless technology which increases the homogeneity within the furnace and reduces the amount of energy required and the operational costs.
tell me more
Industry fact
In 2005 The European Union Emissions Trading System (EU ETS) and the Kyoto Protocol launched the United Nations Framework Convention on Climate Change (UNFCCC).
2010's
Advanced Low Emissions Melting (ALEM) System
Our Advanced Low Emission Melting system is launched. Following the success of the earlier LEAM® system we re-developed the technology and introduced our patented ALEM control system, designed to support the melting of highly contaminated scrap metal.
tell me more
High Yield Burner
Air Products launched the High Yield Burner. A new generation oxy-fuel burner developed specifically to increase yields for rotary furnaces.
tell me more
AOZ burner
We introduced our AOZ burner which gives you the flexibility to use a combination of air and oxygen in your combustion process.
2020's
Tunable Enrichment Air-oxy-Fuel Burner
Fully flexible technology, designed to enhance combustion processes, to be used in combination of air and oxygen in your furnace.
Transient Heating Burner (THB)
Patented technology. Designed specifically for reverb furnaces. This patented technology improves heat distribution across the furnace with the goal of improving energy efficiency and increasing yield.
tell me more
Industry fact
In 2020 the European Union Emissions Trading System (EU ETS) trading period III concludes. If achieved, the proposed caps for 2020 will represent a 21% reduction in greenhouse gases.
Future . . .
Future developments
Air Products has pioneered the application of industrial gas based technologies on both rotary and reverb furnaces and we constantly seek to develop and advance our range.
We pride ourselves on our culture of innovation and continually invest in our research and development capabilities. Our world-class combustion laboratories enable us to help our customers melt and cast more effectively, improve energy efficiency and reduce environmental emissions.
Downstream Processing
In addition to our combustion technologies, we also have a dedicated team of experienced metallurgists. They can work with you to fully understand your metals processing needs and recommend the best solution for your operations.
Annealing
We offer a range of technical gases and process control systems for non-ferrous annealing that can help you maintain the desired atmosphere composition to achieve oxide-free surfaces and consistent metallurgical properties.
tell me more
Extrusion
Our die cooling technology allows you to use liquid or gaseous nitrogen to cool extrusion dies while protecting the surface of the extruded part. The system can help you increase extrusion rates, improve surface quality and increase die life with minimal cost.
tell me more
Powder metallurgy
We offer a full range of technical gases and customised atmosphere solutions for your powder metallurgy applications, including sintering, HIP and spray forming.
tell me more