... for a more productive, efficient and safer facility
The challenges of the past year, from the uncertainty of the pandemic through to the finalisation of Brexit, have brought a period of unprecedented challenge and opportunity to the food industry. For those businesses that have had the agility to ramp up production to meet increased demand, or that have changed their processes to identify a new audience, the results have been rewarding.
The need for an extended shelf life and the heightened attention on site and food safety, together with the public's growing interest in food waste and sustainability, mean there has never been a more complicated time for food manufacturers that are trying to keep their businesses growing. Innovations to bring modern technology into the production process must be a constant focus as companies see the bar raised by competitors.
Now, more than ever, technology needs to come into play to maximise efficiency in the workplace and keep a track on production lines. This includes remote monitoring, using sensors and wireless communications technology to monitor process efficiency, customer production rates, machine settings, parameters and historical data. It allows manufacturers to see whether processes are running as smoothly as they could be or if there is a way to boost efficiency. Data of this kind optimises freezing and chilling processes, saving time and money by providing the information needed to minimise gas usage, while ensuring product quality remains high.
In addition, an overview of how machines are performing helps to guard against unsafe practices and allows for preventative maintenance processes to be carried out before operational failures occur. The ability to diagnose faults remotely reduces downtime and allows for immediate intervention without the need for additional technicians to be brought on-site – ensuring a safe environment and a speedy resolution.
Not only is this a gamechanger in the long term, it will also resonate with those looking to control the number of staff based on-site due to Covid-19 restrictions. Remote monitoring capability means producers can review the efficiency of their operations off-site, checking activity and finding ways to improve productivity while working from home. Unexpected societal events, such as Brexit and Covid-19, continue to affect operations across the sector, and manufacturers have been searching for ways to respond.
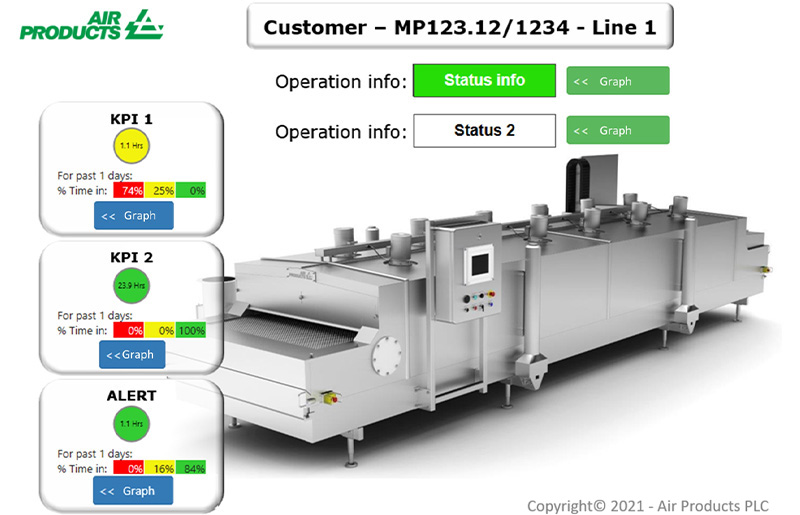
Air Products Process Intelligence (APPI), aims to revolutionise the production line through remote monitoring:
- Increases productivity by up to 25-30%
- Can reduce nitrogen consumption by up to 10%
- Remote access supports safety in your facility